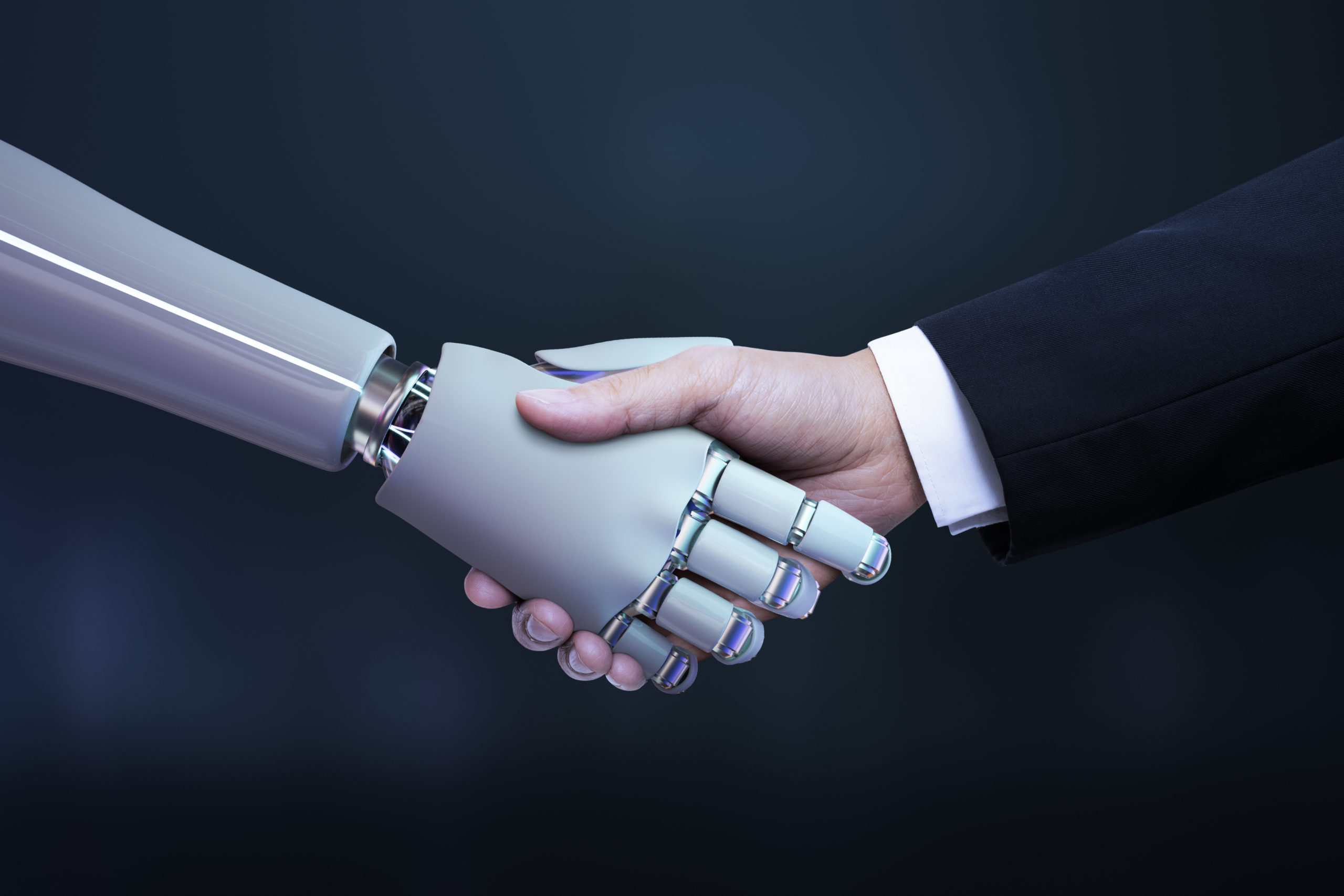
DIGITAL TRANSFORMATION – KEY SUCCESS FACTORS
THE DIGITAL TRANSFORMATION – KEY SUCCESS FACTORS
There are various factors on the path to the smart factory that can lead to either success or failure: starting with the selection of the right software solution in order to control the various processes, to finding a digital strategy tailored to the company.
The development of the digital strategy is accompanied by the development of a future-oriented business model:
This includes, among other things:
– the strategic question of which business areas can be developed in the future
– the new digital orientation of the processes and the optimization of the value chain
– the general consideration of how the services that are offered will be provided operationally – in which processes and with which personnel qualifications.
Based on over 25 years of experience from a wide variety of projects, we have listed here what we consider to be the most important factors that can lead to success or failure.
Selecting the right tools: Software
The consistent digitization and networking of your own manufacturing processes is the basic prerequisite on the way to the smart factory and the optimization of existing processes. When selecting the right software solution for this purpose, two questions are at the forefront:
- what long-term goal – what strategic direction am I pursuing?
- does the software solution offer open interfaces to ensure the necessary flexibility?
Both questions have a decisive influence on the choice of software solution. Especially the topic of open interfaces plays an essential role for the future orientation of the company.
Many solutions offered on the market have their own standard for data exchange or provide only rudimentary information. This can quickly lead to significant new investments, especially in a market environment that is constantly changing. Or in the worst case it will make it impossible to adapt to the changing market situation at all.
The innovative orientation of the software service provider equally has to be considered:
hardly any other industry has undergone such an intensive process of change in recent years as the print and media industry.
The decision in favour of a software solution is accompanied by a considerable investment – and to the same extent for the associated conversion of the existing processes. This usually leads to a long-term business relationship between the software supplier and the print shop: therefore, the willingness on the part of the software service provider to adapt to new and changed market conditions plays a major role.
Staff qualification
In- and externally digitally networked collaboration also requires new work models and new qualification profiles for existing and new staff. In this context, there is much to be said for taking a cue from other industries that have already successfully implemented similar processes.
Successful transformation toward the smart factory requires a flexible operating structure and new qualification models that prioritize collaboration and the implementation of long-term corporate goals at all levels.
In addition to the existing technical skills, IT and problem-solving skills, as well as communication skills, will be required as further key qualifications in all parts of the company in the future.
Routine tasks are being reduced, but the ever-increasing demands from customers along with tight delivery deadlines and often last-minute changes are increasing the need for employees to take responsibility for their own work and their decision-making authority. In the future, it will be necessary for production staff to think entrepreneurially as well.
Qualification and leadership models must be adapted to the changing framework conditions and the factors described must be brought clearly to the foreground.
Company Culture
Ultimately, corporate culture is another important component for a successful digital transformation.
With the successful digital optimization towards a modern printshop, a process has been set in motion that must be continuously developed further: Topics such as product and process innovation will always play an important role.
All employees, not just management, must be motivated to think innovatively and given the necessary freedom to do so. Anyone who is innovative takes risks. This requires a culture of error that must also allow for the possibility of failure.
So how do you get to the point in the company where employees can implement their own ideas and projects and are also allowed to make mistakes in the process?
In every company, departments have different perspectives on problems, tasks and new projects. Therefore, the exchange between the departments is very important.
For example, introduce one innovation day per month!
On this day, all departments can contribute their ideas for improvements in processes or even new product ideas. At the end of the day, a joint decision is made as to which of the projects and suggestions will be implemented.
This simple means leads to employees identifying with the company and being more willing to address critical issues or to develop completely new ideas..
It turns out: many new ideas and business models related to digital transformation are developed in young companies where, instead of rigid hierarchies and linear structures, the working atmosphere is open, communicative, democratic and dynamic in networks (startup culture).
Supply chain management: networking with service providers, suppliers and partners
Despite the challenges that companies in the print and media industry have been facing for years, the area of supply chain management has not yet been subjected to extensive optimization in many companies.
Even today, it is often the manual ordering process where clerks, for example, fax their (paper) orders to their suppliers or place their daily orders by phone. There are always queries, be it regarding the amount of paper available from the supplier, the delivery dates for the material, etc.
Information about stock levels, delivery dates and price calculations is coordinated with the supplier in a time-consuming and ultimately less transparent manner within the company via conventional channels.
Networking with existing service providers, suppliers and partners is therefore another key factor that will determine the success or failure of the smart factory.
There will therefore also be a rethink regarding the selection of suppliers: which interfaces or digital platforms will be made available? Which data / information can be exchanged without effort?
Under certain circumstances, greater savings might be realized through a lean transparent process than through a laboriously discussed cheaper price.
Last but not least: Integration of the customer into the digital network
It is equally true for customers in B2B as well as B2C: digital procurement has become the standard in the private and the commercial sector.
The minimum requirement for a provider is therefore an attractive website or better a web shop, optimally tailored to the customer group that should be addressed.
The close integration of the internal software with the web shop plays an essential role: ideally, the orders are directed online to the company, where they are taken over by the MIS, prepared and fed into the production process. A path that offers enormous savings potential.
The close customer loyalty that can be generated through smooth, convenient processing is also particularly advantageous.
Summary
The continuous networking of all corporate divisions as well as the flexible provision of interfaces, the optimisation of existing internal and external processes as well as the “lived innovation” in the company bring the desired success: cost reduction, efficiency increase, profit maximisation